Plastic Bearing Inserts
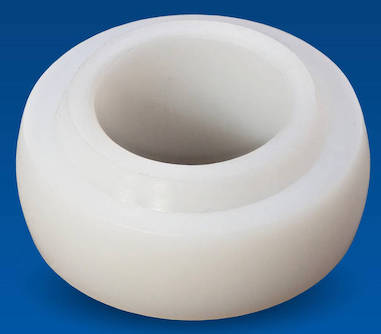 Plastic bearing inserts are designed to replace self-aligning ball or roller bearings with a spherical O.D. within the housing. Our precision plastic bearing inserts are available in UHMW and a high-temp acetal material capable of handling temperatures up to 600°F; we can also supply specific materials and specific sizes that are not listed in the charts below. Our stock sizes range from 1/2" up to 3" inside diameter. Being directly interchangeable with a broad spectrum of brands means these bearing inserts do not require a new or special housing. Plastic bearings are becoming more popular in many industries, such as food and beverage, water treatment, FDA-monitored applications and many more! With superior wear, abrasion, and anti-corrosive characteristics, our plastic bearing inserts have become the top choice for many end-users, resellers, and OEMs alike. Contact our customer support team for pricing and availability.
High Temp Plastic Insert Bearings
Our standard UHMW plastic bearing inserts can handle temperatures up to 200°F; this is the standard for most industrial bearings. In standard circumstances, applications over 200°F and up to 500°F require specific seals, greases, fittings, and housings. However, these additional costs and maintenance can be eliminated with our HT plastic bearing inserts. Our high-temp bearings require no lubrication and can operate in applications exposed to temperatures up to 600°F and retrofit into standard housings. Precision machined from pure virgin high-temp material, these bearings produce a simple solution to a long-standing industry problem.
Plastic Insert Bearing Sizes
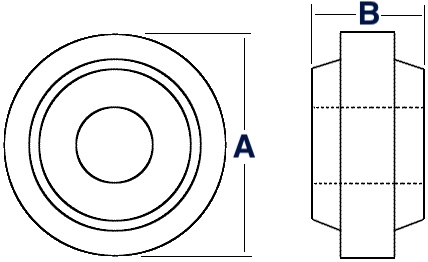
Plastic Bearing Insert Interchange Chart
The chart below shows the interchange data for our plastic insert bearings for the most common bearing manufacturers; this means the housing and associated components will not need to be replaced for additional interchange data on brands not listed below contact our product specialists division for assistance.
Plastic Bearing Insert Speed and Load Data
Determination of the bearing loads, drive factor, and PV value is imperative for new application bearing sizing and selection. The placement of a drive system concerning the bearing supporting it can significantly impact the lives of those bearings; the more even that a load is dispersed over a bearing set, the longer the bearings will last. Formulas for determining bearing loads are shown below.
 Equations for Determining Bearing Loads: L = Total shaft load on bearings (pounds) N = Revolusions per minue r = Radius at which load acts (inches) T = Torque (inch-pounds or foot-pounds) (see below) f = 'f' factor from Driven Factor Table (table below)
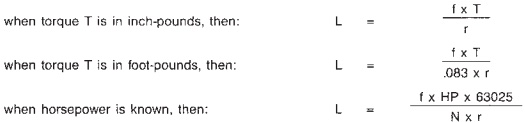 Drive Factor Table ('f')
After the approximate load has been determined (from known data or by using the above formulas), the PV value can be calculated.
Equations for Determining PV Value: P = Bearing Load (psi) A = Bearing Area (square inches) L = Load on Bearing (pounds) V = Velocity of The Shaft (surface feet/ minute = SFM) RPM = Revolutions Per Minute of Shaft D = Shaft Diameter (inches) I = Length of Bushing Through The Bore (inches)
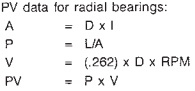 PV Value: The operating PV of a bearing is actually a measurement of temperature. The maximum allowable PV for any situation will vary depending on the thermal and mechanical characteristics of the material selected for the bearing. Because of this, the ambient air temperature of the environment and the corresponding housing temperature is important. Since heat is a major factor in determining the life of a bearing, the ability to dissipate heat through the shaft with a lubricant or by operation in a spray or bath will reduce the bearing failure rate or increase bearing life. Another factor in reducing the life of any bearing is chemical action on a material not suited for such an environment. Any abrasives introduced to a bearing will wear away the bearing material and significantly reduce its life. Most plastic materials will absorb some abrasive particles to a much greater degree than a metal bearing and therefore reduce the damage done to both the shaft and the bearing. Still, it will not totally eliminate that wear.
Plastic Insert Bearing Speed and Load Rating Chart
The data on the below charts is about our UHMW self-aligning inserts in unlubricated conditions. Since the high-end range for operation temperatures on the standard bearings is 180°F to 200°F. Since this material has a low coefficient of friction and thermal conductivity, PV values must be carefully calculated.
The below chart shows information that is calculated as not to exceed the following limits for UHMW insert bearing applications:
- Maximum Pressure (P) = 800 lbs/in
- Maximum Velocity (V) = 50 surface feet/ minute
Note: for UHMW, the combination of PV may not exceed 3000; for PVs that exceed 3000, consult our customer support team for material options. If ambient temperatures are low or the bearing is to be continually operated in water or other liquids and is sufficiently cooled, the PV limits may be increased as long as the bearing temperature is not exceeded. Lubrication can also increase the operating PV limits by providing a lower coefficient of friction on the bearing. It's important to note that our self-aligning plastic bearing inserts are designed to replace self-aligning ball and roller bearing inserts within the same conventional housing. Because our bearings are self-aligned to the same degree as their steel counterparts, no changes are necessary to utilize them within the equipment or bearing housing.
UHMW Bearing Material Data
The term UHMW itself stands for ultra-high molecular material. UHMW material possesses a unique combination of physical and mechanical properties that enable it to perform well under the most rigorous conditions of wear and environment. It has the highest known impact strength of any currently manufactured thermoplastic, plus very high resistance to abrasion against a wide variety of materials. These properties make this material an exceptional option for industrial impact, wear surfaces, and sliding operations. UHMW is also FDA, and USDA-approved for direct contact in food processing applications. For Polyethylene to be certified as UHMW, the material's molecular weight must be at least 4 million (4 PPM). Our UHMW material is certified at 4-6 million molecular weight, and any material with less than 4 million molecular weight is either high-density to low-density (HD or LD) polyethylene. These products are much less expensive to manufacture than UHMW, but the physical properties are correspondingly less. At USA Roller Chain, we certify that only polyurethane greater than 4.2 million molecular weight is used in our plastic insert bearings for the best performance and wear life.
The chart below goes through the specific mechanical properties of our UHMW plastic-bearing inserts.
1. Izod Impact Strength: Samples have two (15° +/- 1/2°) notches on the opposite sides to a depth of 5mm.
2. See the test method description - under sand-slurry test results.
Test Specimens: Dumb-bell type; Duration of Test: 30 days
A. Resistant: Mechanical properties not appreciably affected B. Limited Resistance: Decrease in yield stress and ultimate tensile strength less than 20% C. Not Resistant: Decrease in yield stress and an ultimate tensile strength greater than 20% I. Inorganic Acids
II. Alkalis
III. IAqueous Solutions of Inorganic Salts
IV. Organic Acids
V. Hydrocarbons & Halogenated Hydrocarbons
VI. Alcohol, Ketones, Ester and Amines
VII. Miscellaneous
*The information above and contained herein is, to the best of our knowledge, true and accurate, but all of the recommendations and suggestions are made without guarantee since the conditions of use are beyond our control. We disclaim any liability incurred in connection with the use of these data or suggestions. This publication is not to be taken as a license to operate under or a recommendation to infringe any patents. The observance of all legal regulations and patents is the responsibility of the user.
The abrasion resistance of UHMW is illustrated in the sand-slurry diagram below. These tests were conducted for a period of 7.5 hours at a speed of 1750 RPM. Results for convention wear-resistant materials are expressed as a percentage based on the volume of material lost. A carbon steel standard was assigned a value of 100. The lower values represent an increased resistance to abrasion.
Sand-Slurry Test ResultsIV. Organic Acids
|
|